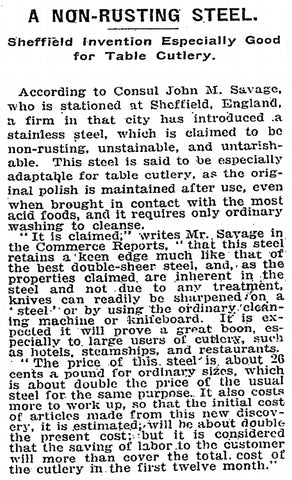
Let’s talk about stainless steel today! We get so many questions that we could write an entire book on this topic. First, let’s offer a very brief history of stainless steel. Stainless Steel is new – barely 130 years old. Between 1904 and 1911, several researchers prepared alloys that could be considered stainless steel today. On October 17th, 1912, engineers Benno Strauss and Eduard Maurer patented austenitic (300 series) stainless steel as Nirosta – only 111 years ago! In 1912 in the USA Elwood Haynes applied for a patent on a martensitic (400 series) stainless steel alloy, but it wasn’t granted until 1919.
The Internet is really cool. The invention of stainless steel was announced in a January 31, 1915, newspaper article in The New York Times (Page 7 of section 8) where it was suggested as being useful for silverware (cutlery). I have included the article here as a historical curiosity.
In the beginning, stainless steel was sold in the US under different brand names including the aforementioned "Nirosta steel." Within the metallurgy industry, however, the name remained undecided; as late as 1921, trade journals were still calling it "unstainable steel," which is a misnomer.
Common Questions About Stainless Steel
Let’s start our discussion with the five most common questions we get asked here at Hardware Everywhere when it comes to stainless steel. Then we’ll move on to the technical section.
1. Is it true that Stainless Steel doesn't rust? That's a commonly believed myth, but it's completely untrue. Almost all alloys of stainless can eventually rust because they contain traces of carbon. Any metal that has traces of carbon can rust. 302, 304, 18-8, and 316 stainless do rust but it takes quite a long time. 410 stainless rusts almost as quickly as steel, but since it's generally surface rust, the integrity of the screw is not usually compromised. “Remember, it's called ‘stain less steel’ and not stains never....” Credit legendary fastener industry giant Wayne Golden for that last sentence.
2. Is it true that all Stainless Steel is non-magnetic? No. In stainless fasteners, 300 series stainless (austenitic stainless steel) is non-magnetic in its raw condition. Cold working it (making the parts) can sometimes cause traces of magnetism in 300 series, depending on various factors, especially in washers. An increase in magnetism is caused by the heat and friction of cold forming, but it does not reduce corrosion resistance. You might get some surface rust, but the part is not rusting internally. A higher proportion of nickel can increase stability in stainless, thus decreasing work hardening and any possibility of magnetism. (For the record 18-8 is a family of stainless steels and includes all alloys from 302 through 305 at the factory's option. Different alloys are used for distinct types of screws. If you want to know what alloy a certain part is, just ask!)
On the other hand, 400 series stainless (martensitic stainless steel) is magnetic just like steel owing to its high carbon content. 500 series stainless is also magnetic, but not typically used to produce fasteners. This article explains it very well.
600 series stainless is non-magnetic as well, but it’s very rare in this industry, and seldom used for fasteners.
Although 304 (A2) and 316 (A4) are classified by many as non-magnetic, that is not the whole story. Stainless Steels are either austenitic, martensitic, or ferritic and mechanical deformation of the stainless steel can cause local changes to the chemical structure from austenitic to ferritic and is why, on occasion, stainless steel can be magnetic - and is the source of much confusion. You will sometimes see an 'L' added to the end of the T316 / T304 designations. So that would be T304L / T316L. The 'L' refers to low carbon. Simply put, the alloy has less carbon than the standard, which gives it slightly better corrosion resistance, but this is coupled with lower mechanical strength properties; further, availability of “L” alloys is almost non-existent off the shelf.
The stronger the magnet, the more likely a non-magnetic alloy will be attracted to a magnet. Even if a magnet does not stick to an austenitic stainless-steel surface, there may still be some magnetic attraction (especially, as we said, in stamped parts such as washers) due to the presence of impurities or surface contaminants. Some rare-earth magnets are extraordinarily sensitive and will stick to the smallest particles.
3. Is 316 stainless stronger than 304 stainless? No, that just isn't true. 316 stainless may be slightly stronger in many applications using larger diameter bolts, but 316 is not stronger in any statistically significant way on most standard sized screws. 316 stainless does, in most but not all applications, exhibit much better anti-corrosive properties but that's not a strength issue. Many people refer to 316 as “marine grade” but that’s a very vague and misleading term. It is typically more corrosion resistant but that’s got nothing to do with strength.
4. Sometimes I see stainless referred to as B8 and B8M. What’s that about? These are ASTM specifications for bolts, rods, studs, and nuts only (typically not screws or washers). By specifying B8 (304) or B8M (316), you will pay a lot more money and wait significantly longer for most of your parts. We recommend, where possible, you avoid them and call out the standard alloy when possible. Only a licensed engineer can determine if that’s acceptable for your intended application. But other B grades (different letters at the end such as B8T) are specialty metals and have no substitutes.
5. Can I tell the difference between stainless and regular steel by looking at it? Sometimes. For bolts, look for head marks which may give you a clue. Often, you can use a magnet to tell 300 series from other grades (300 is usually not magnetic, but as we just discussed, that’s not 100% guaranteed). Stainless tends to have a different reflectivity to the surface. Get two differing parts where you know what material one is and compare them to your unknown sample. That may help. Stainless can tend to feel oiler versus plated bolts.
The Many Grades of Stainless
Hardware Everywhere sells various fasteners in 300 series (302, 304, 316) and 400 series (410, 420, 430) off the shelf. There are so many more grades and each of them has unique metallurgical property for specific applications. The alloys I’ve listed below are just some of the grades we can get. (The ones in blue bold are the most common, but remember not all parts are available in all alloys.)
301 |
403 |
201 |
302B |
17-4PH (630) |
B8 |
302 |
405 |
202 |
302HQ |
17-5 |
B8A |
303 |
408 |
205 |
303Se |
17-7 (316) |
B8C |
304 |
409 |
|
304HQ |
17-7PH |
B8CA |
305 |
410 |
501 |
304L |
18-8 (302) |
B8M |
308 |
414 |
502 |
304N |
|
B8M2 |
309 |
416 |
|
309S |
F593C |
B8M3 |
310 |
420 |
603 |
310S |
F593D |
B8MA |
314 |
422 |
630 |
316F |
F593G |
B8MN |
316 |
429 |
|
316H |
F593H |
B8MNA |
317 |
430 |
904 |
316L |
|
B8N |
319 |
431 |
|
316N |
XM1 |
B8NA |
321 |
434 |
|
317L |
XM7 |
B8P |
329 |
435 |
|
416Se |
|
B8PA |
330 |
436 |
|
420F |
|
B8R |
347 |
440 |
|
430F |
|
B8RA |
348 |
442 |
|
430FSe |
|
B8S |
384 |
444 |
|
440A |
|
B8SA |
|
446 |
|
440B |
|
B8T |
|
|
|
440C |
|
B8TA |
Besides those stainless alloys, many people search for fasteners made from alloys such as Carpenter® 20, Monel® (400 and 500), Inconel®, Hastelloy® C-276, Waspalloy®, and others. These alloys may look like Stainless, but they aren’t – many have some really fantastic and unique metallurgical properties involving heat retention, ductility, and corrosion. We happily supply all those alloys, but they definitely are not stainless. Woldman’s Engineering Alloys is the premiere book on the subject (we use the 6th edition but they’re on the 9th now); if you find this topic as interesting as I do, get this overly technical book for your library. It’s pricey but used copies of older editions are imminently affordable.
Stainless Alloy Composition Table
Metric Grade |
AISI Grade |
Chemical Composition (% maximum unless stated) |
||||||||
C |
Si |
Mn |
P |
S |
Cr |
Mo |
Ni |
Cu |
||
A1 |
SS 202 |
0.12 |
1.0 |
6.5 |
0.20 |
0.15-0.35 |
16.0 - 19.0 |
0.7 |
5.0 - 10.0 |
1.75-2.25 |
A2 |
SS 304 |
0.08 |
1.0 |
2.0 |
0.05 |
0.03 |
15.0 - 20.0 |
0.0 |
8.0 - 19.0 |
4.0 |
A3 |
SS 321 |
0.08 |
1.0 |
2.0 |
0.05 |
0.03 |
17.0 - 19.0 |
0.0 |
9.0 - 12.0 |
1.0 |
A4 |
SS 316 |
0.08 |
1.0 |
2.0 |
0.05 |
0.03 |
16.0 - 18.5 |
2.0 - 3.0 |
10.0 - 15.0 |
4.0 |
A5 |
SS 316Ti (0.5% Ti) |
0.08 |
1.00 |
2.00 |
0.045 |
0.030 |
16.0-18.5 |
2.00-3.00 |
10.5-14.00 |
1.00 |
A8 |
SS 681 |
0.030 |
1.00 |
2.00 |
0.040 |
0.030 |
19.0-22.0 |
6.0-7.0 |
17.5-26.0 |
1.50 |
C1 |
SS 410 |
0.09-0.15 |
1.0 |
1.0 |
0.05 |
0.03 |
11.5 - 14.0 |
- |
1 |
- |
C3 |
SS 431 |
0.17-0.25 |
1.0 |
1.0 |
0.04 |
0.03 |
16.0 - 18.0 |
- |
1.5 - 2.5 |
- |
C4 |
SS 416 |
0.08-0.15 |
1.0 |
1.5 |
0.06 |
0.15-0.35 |
12.0 - 14.0 |
0.6 |
1 |
- |
D2 |
2202 |
0.040 |
1.00 |
6.00 |
0.040 |
0.030 |
19.0-24.0 |
0.10-1.00 |
1.50-5.5 |
3.00 |
D4 |
2304 |
0.040 |
1.00 |
6.00 |
0.040 |
0.030 |
21.0-25.0 |
0.10-2.00 |
1.00-5.5 |
3.00 |
D6 |
2205 |
0.030 |
1.00 |
2.00 |
0.040 |
0.015 |
21.0-23.0 |
2.50-3.5 |
4.5-6.5 |
- |
D8 |
Zeron100 |
.030 |
1.00 |
2.00 |
0.035 |
0.015 |
24.0-26.0 |
3.00-4.5 |
6.0-8.0 |
2.50 |
F1 |
SS 430 |
0.12 |
1.0 |
1.0 |
0.04 |
0.03 |
15.0 - 18.0 |
0.0 |
1 |
- |
Metric Stainless Class Sub-Properties
Both A2 (304) and A4 (316) grades come in three property classes: 50 (soft), 70 (cold-worked), 80 (high-strength), and 100 (extra high-strength) – the most common of which is the 70 class which is cold drawn from bar stock. These classes have different mechanical properties as noted below. (Specify as “A4-70” for example if the grade matters to you. As always, narrowing your specification slows delivery and increases costs.)
Property class |
BOLTS |
BOLTS |
BOLTS |
NUTS |
50 |
500 |
210 |
0.6d |
500 |
70 |
700 |
450 |
0.4d |
700 |
80 |
800 |
600 |
0.3d |
800 |
100 |
1000 |
800 |
0.2d |
1000 |
A2 (18-8) is by far the most common grade of stainless steel fastener sold around the world, accounting for (by some estimates) as much as 80% of all fasteners sold.
Passivation
Passivation, when it comes down to it, is a specialized cleaning process. Almost all stainless is commercially cleaned to remove extraneous iron particles. Some stainless is passivated instead of just being commercial cleaned. The aim of either process is to extend the life of the fastener by inhibiting oxidation causing particles.
Industry standard ASTM A967 defines passivation as, “the chemical treatment of stainless steel with a mild oxidant, such as a nitric acid solution, for the purpose of the removal of free iron or other foreign matter.” ASTM A380 further clarifies passivation as “removal of exogenous iron or iron compounds from the surface of a stainless steel by means of a chemical dissolution, most typically by a treatment with an acid solution that will remove the surface contamination but will not significantly affect the stainless steel itself … for the purpose of enhancing the spontaneous formation of the protective passive film.” Some passivation chemicals are hazardous and unless you have your parts custom made with appropriate certifications; there is no way to know which chemical was used for the passivation process; the three most common are (1) nitric acid, (2) nitric acid with sodium dichromate, and (3) citric acid.
Thread Galling
And we’ll wrap up by discussing thread galling. Galling is an issue that may occur during fastener installation because of the combined effect of adhesion of the metallic surfaces and friction. This ultimately results in the build-up of excessive lumps that can cause additional galling.
Thread surfaces come with small points to create friction when used for fastening. This makes it hard for them to slide over one another without causing damage. The harder the fastener is, the less likely galling is to occur because galling is related to ductility and the more ductile a metal is, the more susceptible the fastener is to galling. Fine threads are far more likely to experience galling than coarser threads.
Thread galling almost always occurs during installation when the threads of a bolt are affected because of excess friction and pressure. This pressure and friction causes the seizing of threads inside a tapped hole. When this happens, it is called “cold welding.” After it occurs, you cannot reverse the damage; you can only cut the bolt out of the hole (or cutting the nut off entirely, if applicable).
To mitigate galling, try to avoid using fasteners that have obviously damaged threads or ones where the nut won’t go on easily. By doing this, you will reduce the possibility of galling. Heat resulting from adhesion and friction is a primary factor of galling. Try to avoid using power tools when installing stainless steel or other materials that are not immune to galling, or use the slowest possible tool setting if you have to use a power tool. You can greatly reduce the likelihood of galling if you use lubricants such as dry wax.
You will find some items like thread cutting screws and self-drilling screws come primarily in 400 series stainless steels because the desire for hardness to make the screws function outweighs the absolute need for corrosion resistance. This isn’t to say you can’t get these parts in 300 series stainless, because you can. But they often don’t work as well. Whereas when it comes to standard bolts, nuts, and washers, those are almost always 300 series stainless because the need for corrosion resistance outweighs the need for hardness. Regardless, every single job is different, so most fasteners come in more than one grade (even in steel this is true). Using anything that is non-standard always comes with a cost penalty, which is often significant.
Item |
300 |
316 |
400 |
Hex Cap Screws |
Common |
Common |
Rare |
Nuts (Hex, Jam) |
Common |
Common |
Rare |
Nuts (Lock) |
Common |
Common |
MTO |
Nuts (All Others) |
Common |
Common |
MTO |
Flat Washers |
Common |
Common |
Rare |
Fender Washers |
Common |
Less Common |
MTO |
Split Lock Washers |
Common |
Common |
MTO |
Star (Tooth) Lock Washers |
Uncommon |
MTO |
Common |
Carriage Bolts |
Common |
Common |
MTO |
Lag Bolts |
Common |
Common |
MTO |
Socket Screws |
Common |
Common |
MTO |
Sheet Metal Screws |
Common |
Less Common |
Less Common |
Self-Drill Screws |
Limited |
Limited |
Common |
Thread Cutting Screws |
Less Common |
MTO |
Common |
Threaded Rod |
Common |
Common |
MTO |
Wood Screws |
Less Common |
Less Common |
MTO |
Deck Screws (Flat) |
Common |
Less Common |
MTO |
Drywall Screws (Bugle) |
Common |
Uncommon |
MTO |
Thumb Screws |
Less Common |
MTO |
MTO |
Cotter Pins |
Common |
MTO |
MTO |
Split Roll Pins |
Less Common |
MTO |
Common |
As always, the standard disclaimer of "not all items are available in all diameters/lengths/threads/materials" applies.